Lights Out, Daten an
Wie der Digitale Zwilling die Automobilindustrie umkrempelt
Daniel Lang, thyssenkrupp, Thomas Bleistein und Robert Becker, August-Wilhelm Scheer Institut
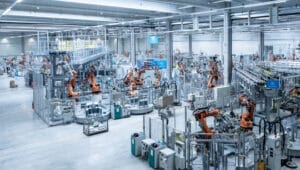
(Titelbild: © thyssenkrupp )
Kurz und Bündig
Die Automobilindustrie muss steigende Anforderungen an Effizienz, Nachhaltigkeit und komplexe Produktionsprozesse bewältigen. Der Digitale Zwilling revolutioniert den Anlagenbau, indem er eine präzise Planung ermöglicht, Nachhaltigkeitskennzahlen wie CO₂-Emissionen integriert und die Zusammenarbeit zwischen allen Akteuren optimiert. Dank standardisierter Datenstrukturen und Plattformen wie Catena-X werden Datenaustausch und Prozessoptimierung deutlich effizienter. So lassen sich bereits in der Planungsphase nachhaltige Entscheidungen treffen und der Carbon-Footprint reduzieren. Der Digitale Zwilling vereint Nachhaltigkeit, Effizienz und Innovation – ein entscheidender Vorteil für die Zukunft der Automobilproduktion.
Die Automobilindustrie durchläuft einen tiefgreifenden Wandel. Was einst nach Science-Fiction klang, ist heute Realität: Produktionslinien, gesteuert von Robotern und digitalen Systemen, arbeiten effizienter und präziser als je zuvor. Doch trotz modernster Technik bleibt ein entscheidender Faktor oft unbeachtet – die Kommunikation und Zusammenarbeit der Menschen. In einer Welt, in der Geschwindigkeit und Flexibilität über den Erfolg entscheiden, stoßen herkömmliche Arbeitsweisen an ihre Grenzen. Der Schlüssel zur Zukunft der Automobilproduktion könnte in einem unsichtbaren, aber mächtigen Werkzeug liegen: dem Digitalen Zwilling.
Moderne Produktionslinien in der Automobilindustrie sind Hightech-Betriebsstätten und wirken heute wie Science-Fiction-Fantasien aus längst vergangenen Tagen. Hunderte von Robotern mit Vorrichtungen und Prozessgeräten führen gemeinsam ein eingespieltes Ballett auf und fügen schließlich aus Tausenden von Blechen ein formschönes Fahrzeug zusammen. Die Kleinteiligkeit des über Fußballfelder verteilten Produktionsequipments gleicht stellenweise der Suche nach der Nadel im Heuhaufen. Fahrerlose Transportfahrzeuge liefern wie von Geisterhand die Einzelteile „just-in-time“ an oder transportieren die Zusammenbauten zur Weiterverarbeitung an eine andere Station. Menschen in der Produktion sucht man teilweise vergeblich. Der hohe Automatisierungsgrad der modernsten Produktionslinien führt schon heute zur „Lights-Out“-Produktion, bei der Fabriken rund um die Uhr ohne menschliche Arbeitskraft betrieben werden – oft im wahrsten Sinne des Wortes mit ausgeschaltetem Licht.
Anlagenbau neu gedacht: Vernetzung als Schlüssel
Damit diese Anlagen Realität werden, müssen bei der Planungs- und Realisierungsphase viele Gewerke Hand in Hand arbeiten. Vom Anlagenbau über die Automatisierungs- und Elektrotechnik bis hin zur Gebäudetechnik sind viele Disziplinen beteiligt. Der heutige Planungsprozess zum Beispiel von Karosseriebauanlagen folgt einem übergeordneten, aber durch die Vielzahl der Komponenten und Planungsbeteiligten sehr komplexen Fabrikplanungsprozess. Die stetige Verkürzung und Parallelisierung der Planungsprozesse bei gleichzeitiger Ausweitung der Variantenplanung mit immer mehr Fahrzeugvarianten auf einer Linie sowie die Verzahnung von Produktentwicklung (Fahrzeugentwicklung) und Prozessplanung (Anlagenentwicklung), das so genannte Simultaneous Engineering, verkomplizieren den Fabrikplanungsprozess erheblich.
Geplant werden solche Produktionslinien daher mit aufwändiger Software wie Computer-Aided Design-Software (CAD-Software) und speziellen Fabrikplanungstools. Um sicherzustellen, dass die Anlagen alle Anforderungen an Taktzeit, Ausbringung, Qualität et cetera erfüllen, werden sie simulativ erprobt, die Pfade der Roboter geplant und die Betriebssoftware „offline“ geschrieben. Mit der virtuellen Inbetriebnahme wird die Planungsphase bereits wenige Wochen nach Planungsbeginn abgeschlossen und mit dem Aufbau auf der Baustelle kann die Realisierungsphase starten.
Moderne Anlagen erfordern eine hochentwickelte Infrastruktur und Technik, doch die Kommunikation und Zusammenarbeit während der Anlagenentstehung bleiben häufig auf einem bescheidenen Niveau. Entsprechend dem Motto „Management mit Tabellenkalkulationen und E-Mails“ ist der Status Quo in vielen Projekten geprägt von der einfachen Übermittlung von Konstruktionsdaten über Datentransfersysteme oder per Excel und E-Mail. Änderungen in der Planung sowie Anpassungen, die von der Baustelle gemeldet werden, werden oftmals in Papierform oder als PowerPoint-Präsentationen verteilt. Diese Form der Dokumentation ist jedoch nicht in der Lage, die notwendige Flexibilität und Aktualität zu gewährleisten, die erforderlich sind, um den dynamischen Anforderungen moderner Produktionslinien gerecht zu werden. Besonders angesichts der fortschreitenden Digitalisierung und der zunehmenden Komplexität der Projekte ist eine Weiterentwicklung der Kommunikationsprozesse dringend notwendig.
Die eingesetzte Software stellt sowohl einen Segen als auch einen Fluch dar. Einerseits erleichtert sie den Experten und Expertinnen die anspruchsvolle Planungs- und Konstruktionsarbeit erheblich, andererseits schränkt sie den Kreis der Nutzenden durch hohe Lizenzkosten ein.
Mit dem Digitalen Zwilling zum Echtzeit CO₂ - Controlling
Das zunehmende Umwelt- und Nachhaltigkeitsbewusstsein der Endverbraucher:innen spielt bei der Kaufentscheidung für ein Fahrzeug eine immer größer werdende Rolle. Diese gesellschaftlichen Anforderungen sowie die regulatorischen Vorgaben der Europäischen Union führen zu einem weiteren Komplexitätszuwachs in der Fahrzeugentwicklung und in weiterer Folge auch in der Anlagenentwicklung. Solche Anforderungen an den Anlagenbau, zum Beispiel hinsichtlich Nachhaltigkeit und Kreislaufwirtschaft des Produktionsequipments, müssen frühzeitig erkannt werden, um im internationalen Wettbewerb nicht den Anschluss zu verlieren und den Anlagenbau am Standort Deutschland wettbewerbsfähig und wirtschaftlich zu halten. Dazu bedarf es jedoch einer umfassenden Unterstützung. Der kollaborative Digitale Zwilling ist hier der Schlüssel. Gepaart mit Künstlicher Intelligenz und einer damit einhergehenden vereinfachten Automatisierung, werden neue Anforderungen zur Nachhaltigkeit kein Mehraufwand, sondern ein Mehrwert.
In Abbildung 1 wird dargestellt, wie neue oder sich geänderte Anforderungen über die Integration von Künstlicher Intelligenz in den kollaborativen Digitalen Zwilling effizient bearbeitet werden und letztlich zu einem stetigen Controlling von Nachhaltigkeitskennzahlen wie beispielsweise dem Product Carbon Footprint beitragen. Ein neuer Soll-Wert durch eine geänderte Anforderung oder Richtlinie wird mit dem Ist-Zustand des Metamodels verglichen und nach einer abschließenden Prüfung freigegeben, und die geforderte Anforderung kann so erfüllt werden, ohne große personelle Kapazitäten zu binden. Status Quo bis dato ist ein händischer Ist-Soll-Abgleich und ein manuelles Anpassen der Prozesse und Software, bis die Anforderung erfüllt werden kann.
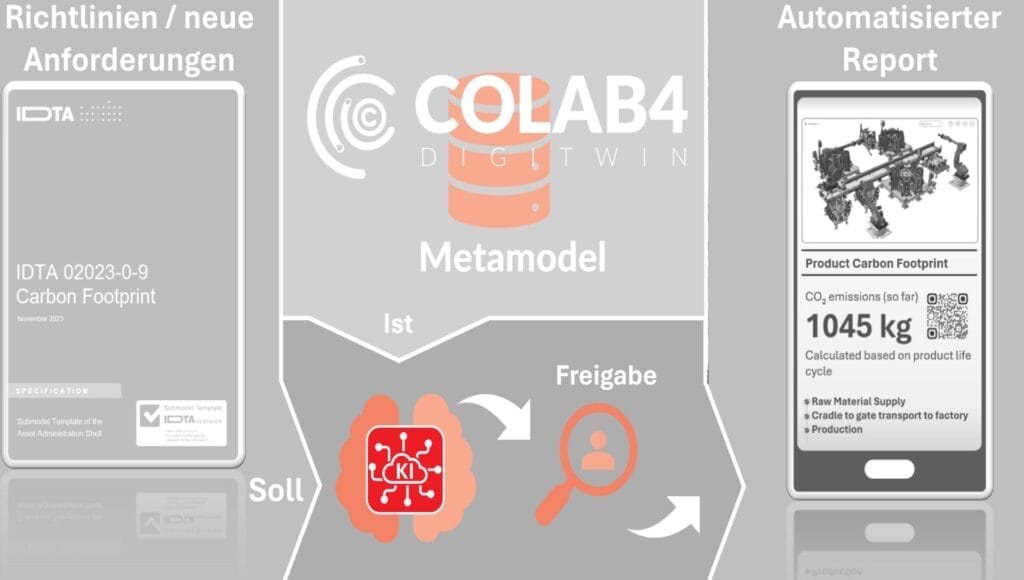
Der Digitale Zwilling, hier einer Produktionslinie, führt alle notwendigen Datenströme in einem virtuellen Abbild zusammen und kann so die mühsame Zusammenarbeit erheblich erleichtern. Jeder Projektbeteiligte verfügt sofort über aktuelle und verlässliche Daten zum Entwicklungsstand. Aufwändige Statusbeschreibungen und das Versenden umfangreicher Konstruktionsdaten entfallen. Auch wesentliche Informationen zur Nachhaltigkeit, wie der CO₂-Fußabdruck von Einzelteilen oder Zusammenbauten, die Recyclingfähigkeit oder Entsorgungshinweise der verwendeten Materialien, sind im Digitalen Zwilling des Produktionsequipments hinterlegt. Um die Effizienzpotenziale voll auszuschöpfen, einen echten kollaborativen Digitalen Zwilling zu schaffen und damit die Transparenz und Effizienz in der Entwicklung zu steigern, sind vor allem standardisierte Datenstrukturen und ein standardisierter Datenaustausch über Unternehmensgrenzen hinweg entscheidend.
Die von der IDTA entwickelte Verwaltungsschale und die zum Beispiel von Catena-X entwickelte Datenraum-Technologie können dabei Schlüsseltechnologien sein, decken sie sich zudem mit der Digitalstrategie der Europäischen Union. Die durch das Bundesministerium für Wirtschaft und Klimaschutz geförderte Initiative „Collaboration for Digital Twin – CoLab4DigiTwin” setzt daher auch bei diesen Technologien an und nutzt den Digitalen Zwilling als Herzstück für die virtuelle Zusammenarbeit aller Gewerke im Anlagenbau. Durch standardisierte Datenstrukturen, das im Projekt CoLab4DigiTwin entwickelte Metamodell sowie eine plattformunabhängige 3D-Darstellung der Konstruktionsdaten wird eine effiziente Zusammenarbeit zwischen den Experten im Büro und den Spezialisten auf der Baustelle erreicht. Der standardisierte Datenaustausch über die Datenraum-Technologie, hier Catena-X, bindet die Zuliefernden standardisiert und global ein. Dies schafft die Basis für gemeinsame gewerkeübergreifende Prozesse sowie KI-basierte Smart Services. Standardisierte Teilmodelle der IDTA sollen die notwendige Interoperabilität sicherstellen.
Durch die schnelle Verfügbarkeit und hohe Datenkonsistenz im kollaborativen Digitalen Zwilling werden Nachhaltigkeitsaspekte bereits während der Anlagenentwicklung deutlich sichtbar. Dies ermöglicht ein aktives CO₂-Controlling, das in dieser Form zuvor nicht umsetzbar war. Fragen wie „Wie viel Druckluft benötigt dieses Equipment?“ oder „Wie hoch ist die elektrische Leistung einer Schweißzange?“ werden heute oft nur grob und häufig überdimensioniert beantwortet, um auf der sicheren Seite zu sein. Mit den präzisen Daten im Digitalen Zwilling kann der Konstrukteur jedoch in Echtzeit den aktuellen CO₂-Fußabdruck der jeweiligen geplanten Zelle einsehen und sich an einem konkreten CO₂-Budget orientieren. Auf diese Weise können Anlagen bereits im Entstehungsprozess sowohl energetisch als auch hinsichtlich Kreislaufwirtschaft und Wiederverwendung optimiert werden.
Durch die Standardisierung der Daten und des Datenaustausches werden vorhandene Informationen effizient zusammengeführt. Dadurch können die Planenden ihre Aufgaben nicht nur präziser, sondern auch mit deutlich geringerem Zeitaufwand erledigen. Der Fokus verlagert sich weg von zeitaufwändigen manuellen Abstimmungen hin zu einer effizienteren datenbasierten Arbeitsweise, die durch neue digitale Werkzeuge zusätzlich unterstützt werden kann.
Alle müssen ihren Beitrag liefern
Durch den hohen Standardisierungsgrad im Automotive-Anlagenbau ist der Anteil an Standardkomponenten und Zukaufteilen besonders hoch. Bei der Planung wird stets versucht, die konstruktiven Bauteile auf die fahrzeugberührenden Komponenten zu reduzieren. Kund:innenspezifische Normen und Freigabelisten legen dabei gezielt fest, welche Zukaufteile verwendet werden sollen. Für den Betrieb erleichtert dies beispielsweise die Ersatzteilhaltung, die Wartung und stellt letztlich auch einen wirtschaftlichen Vorteil dar, da jede Konstruktionsstunde kostspielig ist.
Nachhaltigkeit und Wirtschaftlichkeit sind gesamtgesellschaftliche Aufgaben. Alle an der Anlagenentstehung Beteiligten müssen eng zusammenarbeiten und die neugewonnen Möglichkeiten und Standards nutzen, um eine nahtlose Integration der Daten und ihre spätere Nutzung zu gewährleisten. Dies erfordert nicht nur technische Standards, sondern mehr noch eine Kultur der Zusammenarbeit und des Vertrauens. Eine effiziente und eben nachhaltige Anlagenplanung ist daher nur dann möglich, wenn alle Beteiligten über den Anlagenentstehungsprozess ihren Beitrag leisten und die Komponentendaten entsprechend vollständig und aktuell halten und vertrauensvoll über die Datenräume austauschen. Die föderale Datenhaltung der Verwaltungsschale sowie der unternehmensübergreifende Datenaustausch unterstützen diesen Prozess.
Mit Innovationen zum Green Engineering
Die Transformation der Automobilindustrie erfordert innovative Ansätze und Technologien, um den komplexen Herausforderungen von Effizienz und Nachhaltigkeit gerecht zu werden. Der kollaborative Digitale Zwilling stellt dabei eine Schlüsseltechnologie dar, die es ermöglicht, Produktionslinien bereits in der Planungsphase zu optimieren, ein effizientes CO₂-Controlling durchzuführen und die Zusammenarbeit aller Beteiligten zu stärken. Angesichts der zunehmenden Bedeutung von Transparenz- und Nachhaltigkeitsberichten wird der Carbon Footprint neben anderen Nachhaltigkeitskennzahlen auch für den Anlagenbau unverzichtbar. In Zukunft wird der Digitale Zwilling eine zentrale Rolle spielen. Er wird den automobilen Großanlagenbau so voranbringen, dass er den kommenden Anforderungen gewachsen ist.