Leicht, langlebig, nachhaltig:
Warum das richtige Material den Unterschied macht
Patrick Glöckner, Alejandro Benitez, Sandra Büchs, Evonik
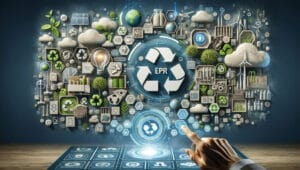
(Titelbild: © Adobe Stock | 729755665 | TechArtTrends )
Kurz und Bündig
Leichtbau und Kreislaufwirtschaft sind zentrale Bausteine für nachhaltige Mobilität. Der Straßenverkehr verursacht weltweit 16 Prozent der CO₂-Emissionen – neue Werkstoffe und Konstruktionsprinzipien können den Energieverbrauch senken. Leichte Verbundwerkstoffe ersetzen schwere Materialien, während Klebstoffe helfen, das Gewicht von Batterien auszugleichen und die Aerodynamik zu verbessern. Kreislaufwirtschaftskonzepte setzen auf recycelbare Materialien und massenbilanzierte Rohstoffe, um Ressourcen effizienter zu nutzen.
Ein Auto ist mehr als sein Antrieb. Ob elektrisch oder mit Verbrennungsmotor – das Gewicht, die Materialien und die Fertigungsweise entscheiden über Effizienz und Umweltbilanz. Während der Fokus meist auf Batterietechnologien liegt, passiert die eigentliche Veränderung in der Materialwissenschaft. Neue Leichtbau-Werkstoffe und clevere Fertigungsprozesse machen Fahrzeuge effizienter und ressourcenschonender. Welche Innovationen setzen sich durch, und wie beeinflussen sie die Mobilität der Zukunft?
Die Transformation der Automobilindustrie ist in vollem Gange. Dabei ist die E-Mobilität ein zentraler Baustein, um die Klimaziele im Verkehr zu erreichen. Sie ermöglicht, die CO2-Emissionen, die durch den Straßenverkehr verursacht werden, drastisch zu reduzieren. Das ist dringend notwendig: Im Jahr 2022 stießen Autos rund 16 Prozent der weltweiten CO2-Emissionen aus, hat die Internationale Energieagentur (IEA) berechnet. Wäre der Straßenverkehr ein Land, läge er noch vor den USA auf Platz 2 der weltweit größten CO2-Emittenten.
Doch der Schwenk zum E-Auto bedeutet mehr als nur ein geändertes Antriebskonzept. Nötig ist ein grundsätzlicher Wandel im Hinblick darauf wie und woraus Auto gebaut werden. Der automobile Leichtbau und die Kreislaufwirtschaft werden zu wichtigen Leitprinzipien: Immer häufiger ersetzen leichte Kunststoffkomponenten schwerere Materialien. Nachhaltigere Werkstoffe gewinnen an Bedeutung.
Verbundwerkstoffe für den automobilen Leichtbau
Konsequenter Leichtbau hilft, die Gewichtszunahme durch die mehrere hundert Kilogramm schweren Traktionsbatterien in Elektrofahrzeugen zumindest teilweise auszugleichen. Das erhöht die Reichweite. Mehr noch: Werden E-Autos von vornherein leichter gebaut, können zum Beispiel Motoren schwächer und Batterien kleiner ausgelegt werden, was wiederum die Ressourcen schont.
Einen besonders großen Beitrag zu künftigen Gewichtseinsparungen könnten sogenannte Sandwichkonstruktionen liefern. Das sind moderne Kohlefaserverbundwerkstoffe mit einem Kern aus besonders leichten Hartschaumstoffen.
Das Chemieunternehmen Evonik stellt zum Beispiel ROHACELL® auf der Basis von Polymethacrylimid und ROHACRYL™ auf der Basis von Acryl her. Bisher wurde ROHACELL® im Automobilbereich in Rennfahrzeugen oder Supersportwagen eingesetzt.
Ein aktuelles Beispiel aus dem Bootsbau verdeutlicht, welch großen Nutzen die Hochleistungsschäume für zukunftsorientierte Mobilitätskonzepte entfalten können: Erst kürzlich hat das britische Unternehmen Falcon Tenders eine Barkasse vorgestellt, deren Dach mit dem nachhaltigen ROHACRYL™ konstruiert und gefertigt wurde. Durch die Verwendung dieses Hochleistungsverbundschaums wurde das Bauteil sogar 75 Prozent leichter als in der Zielvorgabe gefordert – war aber zugleich stabil genug, um den sicheren Einbau von 120 kg Panoramaglas zu gewährleisten. Eine besondere Stärke des Verbundschaumes ROHACRYL™ liegt in seiner Recyclingfähigkeit. Das Polymerdesign ermöglicht perspektivisch, die Bestandteile zurückzugewinnen und somit den Stoffkreislauf zu schließen – eine saubere Lösung am Ende der Lebensdauer.
Dieses Beispiel zeigt, welches Potential Sandwichkonstruktionen bieten, gerade auch wenn es um große Fahrzeuge wie etwa E-Busse geht. Die schiere Größe des Marktes sorgt indes dafür, dass auch die Optimierung vermeintlich kleiner Bauteile unter dem Strich zu signifikanten Verbesserungen führt.
Ein Beispiel dafür sind Gummischläuche für Kühlmittelleitungen. Sie werden zunehmend durch thermoplastische Lösungen mit Hochleistungskunststoffen wie VESTAMID® Polyamid 12 ersetzt. Entsprechende Rohre sind leichter und kostengünstiger und lassen sich nach der Extrusion einfach in Form bringen. Das ermöglicht besonders effiziente platzsparende Lösungen beispielsweise unter der Motorhaube oder im Batteriepack von Elektrofahrzeugen. Thermoplastische Steckverbinder vereinfachen zudem die Montage und beschleunigen so nicht nur den Produktionsprozess der Automobilhersteller, sondern auch Arbeiten in den Werkstätten.
Weitere Einsatzmöglichkeiten für Polyamid 12 ergeben sich aus der Kombination mit anderen Werkstoffen wie Polypropylen. Dünnwandige, dreischichtige Kühlleitungen aus der Materialkombination ermöglichen ein angemessenes Wärmemanagement von Hochspannungsbatterien, Elektromotoren und Systemen. Der Schutz der Bauteile vor Überhitzung und zu großer Kälte ist eine Voraussetzung für den langfristigen und sicheren Betrieb von E-Autos.
Ziel ist, die Temperatur im gesamten Kühlkreislauf nicht über 80 °C steigen zu lassen. Die Batterie-Temperatur sollte für eine optimale Leistung zwischen 20 °C und 40 °C gehalten werden. Die Materialanforderungen, etwa im Bereich Schlagzähigkeit oder Bruchdehnung, sind hoch: Die Kühlleitungen müssen über die gesamte Lebensdauer des Fahrzeugs – mindestens 20 Jahre – funktionsfähig sein, selbst wenn es an heißen Sommern im Freien geparkt wird oder wenn im kalten Winter Rollsplitt von der Straße aufgewirbelt wird und das Material trifft.
Zusätzlich müssen die Kühlleitungen korrosionsbeständig und chemisch stabil sein, um den langfristigen Kontakt mit Kühlmitteln und möglichen Verunreinigungen im System ohne Materialermüdung oder Funktionsverlust zu überstehen.
Klebstoffe ermöglichen Leichtbau
Die konsequente Anwendung von Leichtbauprinzipien erfordert jedoch mehr als nur die Optimierung von Werkstoffen. Auch Kon-struktionsprozesse müssen angepasst werden. Zum Beispiel in der Fügetechnik. Gerade wo Leichtbau und Ästhetik gefragt sind, bieten moderne Klebelösungen entscheidende Vorteile. Wie sehr sich die Klebetechnik bereits durchgesetzt hat, belegen zwei Zahlen, die der Industrieverband Klebstoffe ermittelt hat: Demnach werden rund 15 bis 18 Kilogramm Klebstoff pro Auto verarbeitet. Insgesamt nutzt die Automobilindustrie etwa 9 Prozent der gesamten jährlichen Klebstoffproduktion.
Kleben trägt dazu bei, das Gewicht der mehrere hundert Kilogramm schweren Lithium-Ionen-Batterien in Elektroautos zu kompensieren und so die Fahrzeugleistung beziehungsweise die Reichweite zu erhöhen. Werden beispielsweise Bodenplatten aus Faserverbundwerkstoff durch Zwei-Komponenten-Klebstoffe direkt mit der Aluminiumkarosserie verbunden, spart das im Vergleich zu klassischen Fügeverfahren bis zu 10 Prozent Gewicht.
Klebeverbindungen führen zu mehr De-signfreiheit. Ein Beispiel: Direkt eingeklebte Front- und Heckscheiben erhöhen die Steifigkeit von Karosserien. Hersteller können ihre Fahrzeuge daher windschnittiger konstruieren. Der geringere Luftwiderstand hilft, den Energieverbrauch während der Fahrt zu senken.
Da keine Befestigungslöcher nötig sind, minimiert sich das Korrosionsrisiko. Ein weiterer Vorteil ist, wenn unterschiedliche Werkstoffe zusammengefügt werden, ist die dauerhafte Flexibilität der Verbindung. Die Spannung wird über die gesamte Klebefläche gleichmäßig verteilt, Spannungsspitzen werden vermieden.
Dabei ändern sich die Anforderungen an einen Klebstoff je nach konkretem Anwendungsfall: Mal ist hohe Festigkeit gefordert, mal hohe Widerstandskraft gegen aggressive Flüssigkeiten oder permanente UV-Bestrahlung durch Sonnenlicht. Immer mehr rückt auch die Wiederverwertbarkeit von geklebten Materialien in den Fokus (Rezyklierbarkeit), etwa indem die Klebung reversibel gestaltet wird. Chemieunternehmen wie Evonik bieten ein breites Portfolio an speziell abgestimmten Additiven, Bindemitteln und weiteren Komponenten. Nur deshalb können Klebstoffe gezielt für den späteren Anwendungsfall optimiert werden.
Kreislaufwirtschaft: Am Anfang an das Ende denken
Innovative Leichtbauverfahren können den Klimafußabdruck eines Fahrzeuges in der Nutzungsphase maßgeblich verbessern. Der Anspruch, den viele Fahrzeughersteller an sich selbst stellen, ist jedoch längst höher: So hat sich die deutsche Automobilindustrie zum Ziel gesetzt, eine vollständig klimaneutrale Mobilität bis spätestens 2050 zu ermöglichen – im Einklang mit dem Pariser Klimaschutzabkommen.
Ohne Kreislaufwirtschaft dürfte diese Vision kaum Realität werden. Zwar fallen dank alternativer Antriebe CO2-Emissionen während des Betriebes kaum noch an. Dafür fallen künftig jene Emissionen stärker ins Gewicht, die bei der Rohstoffgewinnung, ihrer Verarbeitung, während der Fahrzeugproduktion und am Ende des Nutzungszyklus entstehen.
Daher ist es unumgänglich, dass Strategien zur CO2-Reduktion über die Nutzungsphase der Fahrzeuge hinausgehen und alle Wertschöpfungsstufen in den Blick nehmen. Genau das spiegelt sich im Konzept einer Kreislaufwirtschaft wider.
Um Materialkreisläufe zu schließen, gilt es, das Nutzungsende eines Produktes von Anfang an in den Blick zu nehmen. Das gelingt mit Ansätzen wie dem „Design for Circularity“: Ziel ist, Produkte so zu gestalten, dass sie möglichst einfach und vollständig rezykliert werden, damit sie als Ausgangsmaterial für ein neues Produkt dienen können. Evonik hat in einer Studie zu einem Monomaterial-Autositz vorgemacht, wie dieser Ansatz exemplarisch im Automotive-Bereich umgesetzt werden könnte.
Autositze müssen komplexe Anforderungen erfüllen. Stabil und robust soll das Gerüst sein, gleichzeitig braucht man eine Lehne, die Halt gibt und vieles mehr. Normalerweise werden daher zahlreiche unterschiedliche Kunststoffe mit weiteren Materialien wie Stahl kombiniert. Diesen Mix für das Recycling wieder aufzutrennen, ist aufwendig. Gemeinsam mit Ingenieuren von VESTARO haben die Kunststoffexperten von Evonik daher einen Demonstrator entwickelt, bei dem alle Komponenten eines Autositzes wie harte Schalen, Schaumstoffe, Vliese oder Fasern aus Polyamid 12 gefertigt waren.
Massenbilanzierung ebnet nachhaltigen Rohstoffen den Weg
Spezialchemiekonzerne wie Evonik können den Aufbau einer Kreislaufwirtschaft auf verschiedenen Ebenen vorantreiben. Zum Beispiel, indem sie die eigene Rohstoffbasis ändern: Längst hat das Essener Unternehmen etwa zirkuläre Polyamide im Angebot. Hier werden in einem Massenbilanzansatz alternative Rohstoffe wie Pyrolyse-Öl aus Altreifen oder gebrauchtes Frittenfett verwendet. Im Vergleich zur regulären Produktion eines Standardmaterials verbessert sich der ökologische Fußabdruck hier zum Beispiel um 70 Prozent. Aufgrund der komplexen Wertschöpfungsketten ist es gerade in der Chemieindustrie in der Regel ökonomisch wie ökologisch nicht möglich, eine eigene Infrastruktur nur für nachhaltige Rohstoffe zu schaffen. Hier setzt das Bilanzierungsprinzip der Massenbilanz an, dass die Einsatzstoffe mit den Ausgangsprodukten von Produktionsprozessen vergleicht. Dies gewährleistet, dass nachhaltige Endprodukte mit der eingekauften Menge an nachhaltigen, also zum Beispiel rezyklierten oder biobasierten Ausgangsstoffen übereinstimmen. Der gesamte Prozess wird von einer unabhängigen Stelle nach den international anerkannten Standards wie etwa ISCC oder REDCert überprüft und zertifiziert. Durch strenge Buchführung und externe Audits ermöglicht der Massenbilanzansatz somit nachhaltige Produkte in großem Maßstab. Es entstehen kosteneffiziente Lösungen, wobei jedes eingesetzte erneuerbare Molekül rückverfolgt werden kann.
Isophoron-basierte Materialien aus erneuerbarem Aceton ermöglichen im Automobilbau hochwertige Verkleidungen und Instrumententafeln. Sie sind chemisch identisch mit fossilen Varianten, ebenso leistungsfähig und senken den fossilen Kohlenstoffanteil um bis zu 100 Prozent. Angesichts steigender Anforderungen an nachhaltige Mobilität bleiben Leichtbau und Kreislaufwirtschaft zentrale Faktoren für effizientere und umweltfreundlichere Fahrzeuge.