Hyperautomatisierung ist...
wenn die Dunkelfabrik sich selbst organisiert.
Christian Bennoit und Tobias Greff, August-Wilhelm Scheer Institut für digitale Produkte und Prozesse
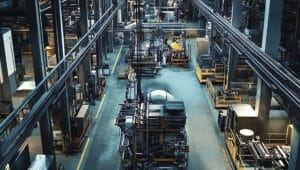
(Titelbild: © AdobeStock | 931627259 | Oleh)
Kurz und Bündig
Hyperautomatisierte Fabriken sind die nächste Generation vollautomatisierter Fabriken nach „Dunkelfabriken“. In der Theorie steuern, überwachen und organisieren sie sich völlig selbstständig. Was bleibt sind die durch Menschen zu treffenden Entscheidungen. Zumeist sind diese strategischer Natur. Dabei sind die Optimierungsparameter zu definieren: Wieviel gewichtet die eigene Organisation ökologische, soziale, ökonomische, ethische, sicherheitstechnische oder datenschutztechnische Parameter? Doch bevor man hier nur noch dashboardzentriert steuert, muss dies in einem wertschöpfungskettenübergreifenden, intelligenten Netzwerk – einem steuerbaren, geteilten Datenraum – umgesetzt werden. Datenflüsse, Abhängigkeiten, intelligente Vertragskonstrukte und Prozesse müssen beschrieben werden. Hier setzt eine Referenzmodellierungsmethode für hyperautomatisierte Prozesse an, welche durch die Autoren entwickelt wurde und hier vorgestellt wird.
Es ist dunkel in der Produktionshalle, doch die Anlagen arbeiten auf Hochtouren: Sensoren blinken, Kompressoren brummen, Energieketten summen. Transportroboter bewegen sich autonom über den Hallenboden. Sie versorgen die Produktionslinien just-in-time mit Rohmaterial und transportieren Zwischenprodukte zur nächsten Station. Am Ende werden die fertigen Produkte automatisiert für den Versand verpackt. Die Schicht endet produktiv, die Kennzahlen bestätigen es. Ein autonomer Schichtwechsel steht bevor – doch wer kommt und wer geht?